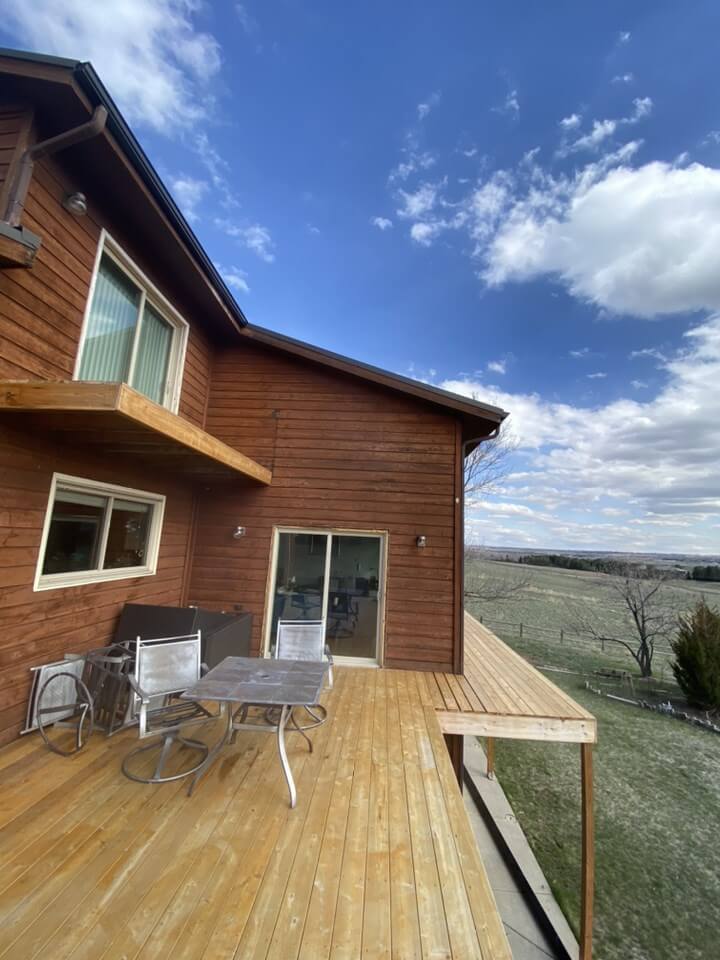
Project Summary: Ace of Diamonds Painting was originally contacted in February to come look at the project. The homeowners had been dealing with the insurance since 2019 to recover losses caused by a hail storm. At the initial arrival it was clear that hail had damaged the stain and paint on the home. Unfortunately, the insurance had not accounted for this in their original adjustment quote. The main issue was, in order to have the new stain applied properly and evenly we would need to strip the siding back to bare wood on all sides. So, our next step was to create a detailed quote and video synopsis to submit to the insurance company and have them add this to the claim.
Ultimately, the claim went through and the homeowners contracted with us to start the work. We were thrilled to have the opportunity to take on this awesome restoration and transformation project!
Project Requirements: From the beginning the Homeowners had a very specific design they wanted to accomplish with the finished product that was actually pulled from the cover of an architectural magazine. They had colors picked for the fascia, soffit trim, eaves, windows, siding lime washing of brick and the cedar siding. All of the fascia trim needed to be sanded, full primed and caulked as it had never been painted before. The eaves had previously been painted so they just needed to be recoated. The 1x2 soffit board that bordered the eaves around the entire home needed to be painted black, so, it needed to be tape caulked, primed, caulked and painted as it had never been painted before either. There were several cedar beams that needed to be sanded to bare wood, patched in some areas and washed with oxalic acid prior to staining. Some of the windows were being replaced due to the damage caused by hail and some were staying, therefore the paint needed to closely match the other windows. Because of the extensive damage caused by hail to the cedar siding we needed to strip and remaining stain off and get down to bare wood. Step 1 for this was to mix the Super Deck Restoration concentrate into a pump spray bottle with water and spray small sections with the contents, as the contents will lose their effectiveness as they dry out. Then we washed the product off completely using a pressure washer about 6-9 inches from the surface. Because of the shape of the home, we needed to rent a 4x4 boom lift to complete this on all areas safely and successfully. The Lime washing was all done by hand with a lot of input from the homeowner in order to get the exact look they were hoping for.
We used Sherwin Williams Duration Gloss for all of the fascia and Soffit trim. Sherwin Williams Duration satin for the eaves, Super Deck semitransparent for the stain and Romabio lime wash for the lime wash.
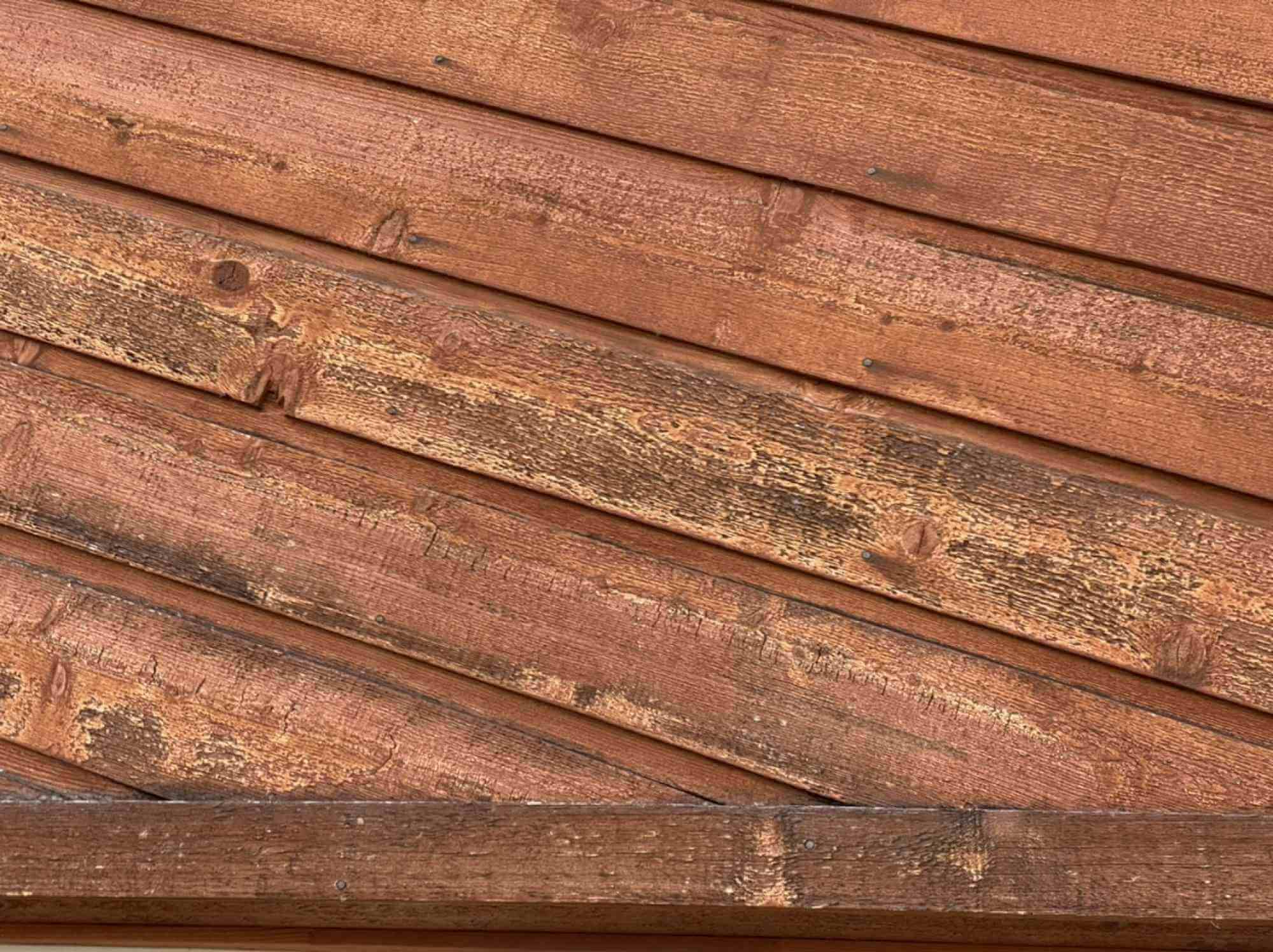
Challenges: There were many challenges on this job. The first was finding the exact right combination and timing of the stripping, pressure washing and oxyalic acid to get the wood were it needed to be. Additionally, one of the big concerns of the homeowners was that if we washed to close we may damage the wood. There was some question as to whether the right product had been chosen to complete the job. Another painting contractor had told them that if the right product was chosen that it would wash right off with a hose. After 1 day of working and some additional research by the homeowner we decided to order the product the other contractor suggested. Only one issue with this, we had to have it shipped freight from Minnesota, as we don't have a freight shipping dock this was a challenge. After some phone calls, one of our gracious local vendors allowed us to have it shipped to them to be picked up by us upon receipt. This put the project on a complete stand still and after a week and a half we had the new stripping product. One of the issues this caused is that the project was now being worked on in the hottest part of the year, getting above 90 degrees before 10am causing the stripper to dry out rapidly. Once we finally received the new product we tried a large area with high hopes, only to find that it did not work as good as the product we had already been using. After all this, the homeowner agreed to let us experiment without intervention on one section of the house, and we got it exactly right.
The next biggest change was the new roof that had been installed was a beautiful steel roof and very slippery when dusty or wet. The constant water from the pressure washer meant we could not be on the roof really at all while washing, thus, we had a 40 foot boom lift to lift us in place.
This was a huge help, however the uneven terrain and awkward angles made navigating the lift no easy task in it of itself. The other challenge working in an efficient manner on the project, we had a crew of 3 and the stripping was really only a 2 man job. So in order to keep the project on track one of the guys started working on the deck skirt that did not need to be stripped down, but did need to be primed and painted. Once more of the stripping was complete he was able to move to the eaves, fascia, and later the intricate soffit trim board. By doing this we knew we would have to come back and mask theses areas off prior to applying the stain to the body. After the stripping was complete there was some decent clean up needed before we could get to staining, luckily the piles of the stripped off remnants could be picked up in large chunks, however, several areas needed to be pressure washed including the brick in order for the lime wash product to adhere. Last but not least, the product we need to do the lime washing is manufactured in Italy. Being that we were still in the middle of a pandemic and Italy was one of the first places to have the most cases, their plant was totally shut down causing the product to be on severe back order. The product we ordered 2 weeks before the original start date was now scheduled to arrive 3 weeks after we were planning to finish. This left us no other option but to finish everything we could and come back once we had the product in hand. The hardest part to believe is that once we received it, it was the wrong color! Thankfully, after doing some research the base we had could be tinted at a local store with an exact right kin of tint. At that point, the biggest concern was having enough and completing the job before the homeowners left for their month long vacation the following week. No pressure right? Well, we had enough and finished the job to ours and the homeowners great delight.
Outcome: Overall, the project was completed to the highest standards and exceeded the customers expectations. And to our astonishment, the house resembled the one from the architectural magazine cover very accurately. The end result was one of the most gratifying experiences we have had to date.
Not to mention, even with all of the challenges, the deadline was ultimately met and EVERYONE, was able to go on their vacations